En el panorama de fabricación actual, que evoluciona rápidamente, el concepto de fábrica inteligente ha surgido como un cambio de juego para las empresas que buscan optimizar sus operaciones y mantenerse por delante de la competencia. A la vanguardia de esta transformación se encuentra el sistema Smart Factory Manufacturing Operations Management (MOM), que ofrece una gama de potentes funcionalidades para optimizar los procesos, mejorar la eficiencia e impulsar la innovación.
En esta publicación de blog, profundizaremos en uno de los módulos críticos del sistema Smart Factory MOM, el módulo de Programación. Al explorar sus aplicaciones prácticas, nuestro objetivo es mostrar cómo este módulo puede revolucionar la programación y ejecución de la producción, permitiendo a los fabricantes alcanzar sus objetivos operativos sin problemas.
Pero antes de profundizar en las complejidades del módulo de Programación, tomemos un momento para comprender la esencia de una Smart Factory MOM y cómo permite a los fabricantes optimizar sus operaciones. Desarrollada por eWorkplace Manufacturing Inc., la solución Smart Factory MOM es una plataforma configurable y plug-and-play que aprovecha las funcionalidades basadas en la nube para impulsar la eficiencia, la sostenibilidad y la innovación en toda la organización.
Smart Factory MOM está diseñado para abordar los desafíos comunes que enfrentan los fabricantes, incluidos los sistemas manuales, la dependencia de las hojas de cálculo, los problemas de calidad, los problemas de gestión de activos y mano de obra, las complejidades de cumplimiento y muchos más. Con un enfoque en la resolución de problemas y la mejora continua, esta solución permite a los fabricantes lograr una fabricación inteligente al optimizar la eficiencia, mejorar la productividad, garantizar la visibilidad y minimizar el desperdicio.
Para lograr estos objetivos, Smart Factory MOM emplea cuatro capacidades clave: Visualizar, Simular, Ejecutar y Adquirir.
- El componente Visualizar proporciona a los responsables de la toma de decisiones y a los equipos de operaciones información en tiempo real sobre los procesos de fabricación, lo que ofrece una mayor visibilidad y conocimiento.
- A través de la función Simular, los fabricantes pueden anticipar y responder rápidamente a las variables cambiantes, los requisitos del mercado y las demandas de los clientes aprovechando las potentes capacidades de simulación.
- La capacidad de Ejecución permite a los fabricantes tomar decisiones informadas, optimizar la utilización de activos y empleados, reducir los costos de producción, disminuir el tiempo de entrega y minimizar el desperdicio.
- Finalmente, la funcionalidad Adquirir permite una conectividad perfecta con maquinaria y dispositivos de automatización, lo que facilita la gestión centralizada de datos y mejora la productividad y el rendimiento en el taller.
Ahora que hemos establecido la importancia del sistema Smart Factory MOM, dirijamos nuestra atención al módulo de Programación. Este componente crítico juega un papel fundamental en la programación y ejecución eficiente de la producción.
¿Listo para descubrir las ventajas únicas de convertirse en nuestro socio de canal? Programe una reunión con nuestro equipo ahora y conozca nuestra última solución Smart Factory.
AGENDAR UNA CITA
Módulo de Programación: Propósito e Importancia
El módulo de Programación es una parte integral de Smart Factory MOM. El módulo de Programación utiliza un sofisticado sistema de planificación y programación llamado Opcenter Advanced Planning and Scheduling (APS). Este sistema avanzado de planificación y programación opera a través de un enfoque de programación estratégica basado en restricciones, lo que permite la generación de programas de producción de manera integrada y computarizada.
El módulo de Programación tiene como objetivo permitir que los fabricantes optimicen sus programas al incorporar todos los requisitos y objetivos de programación en un motor centralizado. Esto garantiza que las actividades de producción se planifiquen y coordinen estratégicamente para maximizar la eficiencia y la utilización de los recursos. Además, el módulo de Programación permite modificar el programa de producción a lo largo del día, lo que permite ajustes en tiempo real en respuesta a las circunstancias cambiantes.
¿Cómo puede ayudar el módulo de Programación a lograr una programación de capacidad finita para los fabricantes?
La programación eficiente de la producción y la satisfacción de la demanda de los clientes son cruciales para los fabricantes en el competitivo mercado actual. Sin embargo, muchos fabricantes luchan por evaluar su capacidad de producción con precisión y optimizar sus operaciones en consecuencia. Para hacer frente a este desafío, la implementación de la programación de capacidad finita es clave.
Analicemos un problema de fabricación, la solución a ese problema y cómo los fabricantes pueden aprovechar el módulo de Programación para lograr una programación de producción eficiente y mejorar su rendimiento operativo general.
El problema de la fabricación
Los fabricantes enfrentan un desafío importante para satisfacer la demanda de los clientes y garantizar procesos de producción eficientes. A menudo tienen dificultades para evaluar su capacidad de producción con precisión y fabricar productos de manera eficiente dentro de sus límites de capacidad. Retrasarse en los pedidos de los clientes y no cumplirlos a tiempo se convierte en un problema común. Los fabricantes necesitan una solución que pueda calcular su manejo de capacidad y les permita satisfacer la demanda de los clientes rápidamente.
La solución: programación de capacidad finita en una Fábrica Inteligente
Para superar estos desafíos, los fabricantes pueden implementar la programación de capacidad finita como la solución definitiva. La programación de capacidad finita considera restricciones de capacidad predeterminadas, como horas de trabajo, turnos y horas de funcionamiento de la máquina. Al aprovechar el módulo de Programación, los fabricantes pueden optimizar su programación de producción en función de la información de capacidad en tiempo real.
¿Cómo pueden los fabricantes aprovechar la programación de capacidad finita a través del módulo de Programación en Smart Factory MOM?
1. Defina con precisión la capacidad de las máquinas y los empleados
el módulo de Programación en Smart Factory MOM permite a los fabricantes definir claramente la capacidad disponible en sus máquinas y empleados. Esta definición precisa de la capacidad evita la planificación basada en suposiciones y garantiza un programa de producción más fiable.
2. Considere las restricciones de recursos
el módulo de Programación incorpora restricciones de recursos en el proceso de programación. Considera factores como la disponibilidad de la máquina, los turnos de los empleados, las pausas para el almuerzo y el tiempo de inactividad aceptable . Al considerar estas restricciones, los fabricantes pueden programar operaciones solo cuando los recursos están disponibles, evitando sobrecargas y cuellos de botella.
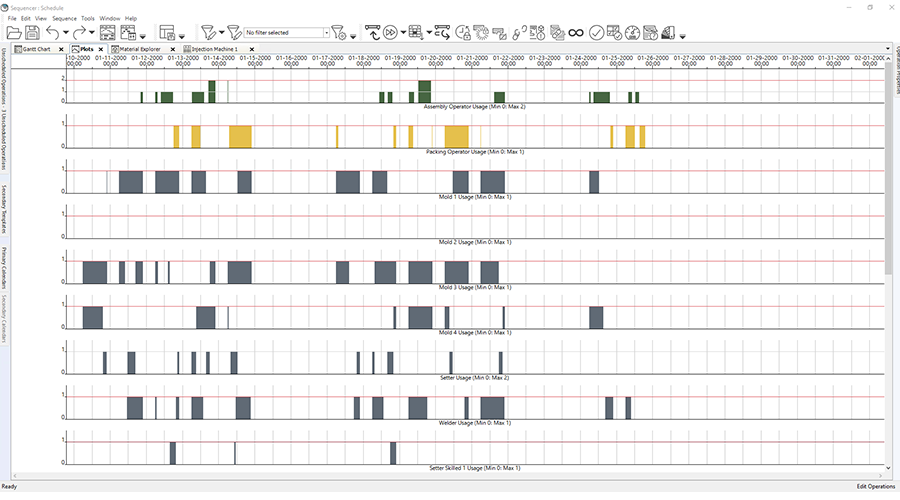
3. Optimice los cronogramas y priorice los proyectos
con la programación de capacidad finita, los fabricantes pueden optimizar los cronogramas de producción para utilizar las horas productivas de manera más eficiente. El módulo de Programación ayuda a asignar recursos de manera efectiva al priorizar proyectos en función de la disponibilidad de recursos. Esto permite a los fabricantes optimizar los procesos, asignar los recursos de manera adecuada y mejorar la eficiencia general de la producción.
4. Prevenga problemas y mejore el control de costos
los fabricantes pueden predecir y prevenir problemas potenciales que pueden surgir debido a una planificación de capacidad inadecuada. Este enfoque proactivo garantiza que los plazos se cumplan con mayor competencia y minimiza el riesgo de pérdida de inventario. Además, los datos de producción precisos recopilados a través del módulo ayudan a los fabricantes a mejorar el control de costos y optimizar la utilización de recursos.
5. Mejore la experiencia del cliente y las entregas
la programación de capacidad finita permite a los fabricantes brindar una mejor experiencia al cliente al cumplir con los plazos de entrega de manera constante. El módulo de Programación ayuda a agilizar los procesos, evitar retrasos y respaldar entregas más rápidas. Compartir datos de producción precisos con los clientes mejora la transparencia y genera confianza.
Diagrama de Gantt: un camino hacia la programación óptima

En la búsqueda de una programación de producción eficiente y una utilización optimizada de los recursos, el módulo Programación ofrece una herramienta valiosa, conocida como diagrama de Gantt. El diagrama de Gantt representa visualmente el cronograma de producción, mostrando tareas, recursos y sus respectivos cronogramas. Desempeña un papel crucial para ayudar a los fabricantes a aprovechar la programación de capacidad finita de manera efectiva. Algunos de los puntos clave sobre los diagramas de Gantt incluyen:
1. Visualización del programa de producción
el diagrama de Gantt proporciona a los fabricantes una visualización clara e intuitiva del programa de producción. Muestra tareas, sus horas de inicio y finalización, dependencias y asignaciones de recursos. Con esta representación visual, los fabricantes pueden comprender fácilmente la línea de tiempo general, identificar rutas críticas y evaluar la asignación de recursos de un vistazo.
2. Utilización eficiente de recursos
la programación de capacidad finita considera los recursos disponibles y sus capacidades al crear un programa de producción. El diagrama de Gantt dentro del módulo de Programación permite a los fabricantes asignar recursos con precisión. El diagrama de Gantt ayuda a identificar sobrecargas, cuellos de botella o recursos infrautilizados al representar visualmente la utilización de recursos en todas las tareas y el tiempo. Los fabricantes pueden tomar decisiones informadas para equilibrar las cargas de trabajo, ajustar los cronogramas y optimizar la asignación de recursos, lo que garantiza un uso eficiente de la capacidad finita.
3. Ajustes de programación interactivos
una de las ventajas clave del diagrama de Gantt es su naturaleza interactiva. Los fabricantes pueden modificar el cronograma directamente dentro del gráfico, haciendo ajustes basados en datos en tiempo real o cambiando prioridades. Simplemente arrastrando y soltando tareas o ajustando su duración, los fabricantes pueden evaluar diferentes escenarios, simular escenarios hipotéticos y realizar cambios de programación dinámicos. Esta flexibilidad permite a los fabricantes responder a eventos inesperados, pedidos urgentes o limitaciones de recursos, manteniendo el equilibrio general del programa de producción.
4. Análisis de la ruta crítica
el diagrama de Gantt proporciona un análisis de la ruta crítica, destacando las tareas o secuencias de tareas que determinan el cronograma general del proyecto. Al identificar la ruta crítica, los fabricantes pueden concentrar sus esfuerzos en garantizar que estas tareas se ejecuten de manera eficiente y sin demoras.
5. Colaboración y comunicación
el diagrama de Gantt es una herramienta de comunicación y colaboración dentro del sistema Smart Factory MOM. Permite a las partes interesadas, incluidos los gerentes de producción, los operadores y otros miembros del equipo, visualizar y discutir el cronograma de producción. Al compartir el diagrama de Gantt, todos los involucrados obtienen una comprensión compartida de la línea de tiempo, la asignación de recursos y las dependencias. Esto facilita una mejor coordinación, toma de decisiones y colaboración entre funciones, fomentando un entorno de producción más ágil y receptivo.
Capacidades de APS: ejemplo del mundo real
Siemens, líder mundial en tecnología industrial, enfrentó desafíos para optimizar la productividad de su centro de tratamiento de superficies de carrocerías de vagones. Siemens utilizó Opcenter APS, una poderosa solución avanzada de planificación y programación, para acelerar el tiempo de producción, reducir los cuellos de botella y evitar entregas tardías. Al integrar la programación en su proceso de producción digital y aumentar el nivel de detalle en el proceso ERP, Siemens pretendía coordinar el control del rendimiento y mejorar la productividad general. Este estudio de caso destaca los desafíos enfrentados, las claves del éxito en la implementación de Opcenter APS y los impactantes resultados logrados.
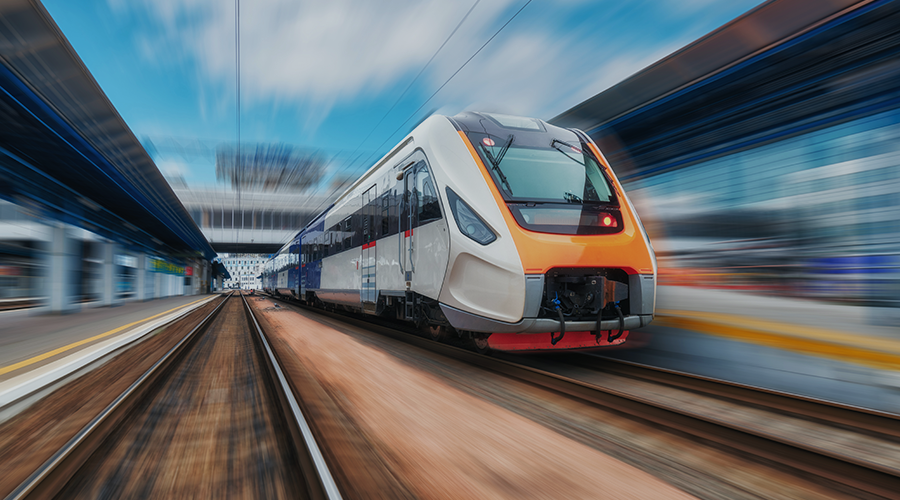
Desafíos
Siemens identificó varios desafíos en su centro de tratamiento de superficies de carrocerías de vagones. Necesitaban acelerar el tiempo de procesamiento de los tratamientos superficiales de la carrocería de los vagones, reducir los cuellos de botella en el proceso de fabricación y garantizar las entregas a tiempo. Estos desafíos requerían una solución integral para optimizar la programación y la coordinación en toda la línea de producción.
Claves para el éxito
Para superar los desafíos, Siemens implementó Opcenter APS. Los siguientes factores jugaron un papel crítico en su éxito:
1. Integración de la programación
Opcenter APS integró perfectamente la programación en el proceso de producción digital de Siemens. Esto permitió la coordinación de actividades en tiempo real y la utilización eficiente de los recursos, optimizando el flujo de fabricación general.
2. Proceso ERP detallado
Siemens aumentó el nivel de detalle en su proceso ERP. Al incorporar datos completos, obtuvieron una mejor visibilidad de las operaciones de fabricación y pudieron tomar decisiones de programación más informadas.
3. Control y coordinación del rendimiento
Opcenter APS permitió a Siemens coordinar los datos de rendimiento con los tiempos de proceso y secado. Esta sincronización aseguró un progreso fluido en los diversos pasos de trabajo involucrados en el tratamiento de la superficie de la carrocería del vagón, minimizando el tiempo de inactividad y maximizando la productividad.
Resultados
La implementación de Opcenter APS proporcionó mejoras significativas al centro de tratamiento de superficies de carrocerías de vagones de ferrocarril de Siemens. Los resultados clave logrados incluyen:
1. Reducción del trabajo sin valor agregado
con Opcenter APS, Siemens redujo el trabajo sin valor agregado en un 60 % y el tiempo de preparación en un 10 %. Esta optimización agilizó el proceso de fabricación, ahorrando tiempo y recursos.
2. Productividad y eficiencia mejoradas
la implementación exitosa de Opcenter APS permitió a Siemens lograr mejoras notables en productividad y eficiencia. Con una programación optimizada, podrían cumplir con los objetivos de producción de manera más consistente y eficiente.
3. Reducción de costos
mediante una programación y coordinación precisas, Siemens experimentó una reducción en los costos de incumplimiento. Los cronogramas precisos permitieron una mejor asignación de recursos, minimizando las interrupciones y el retrabajo.
Pensamientos finales
El motor Opcenter APS impulsa el módulo de Programación en Smart Factory MOM y es fundamental para ayudar a los fabricantes a lograr programas de producción óptimos de manera más rápida y efectiva. Al aprovechar los datos en tiempo real, las operaciones optimizadas y la agilidad mejorada, las capacidades de Opcenter APS permiten a los fabricantes superar los desafíos de producción, aumentar la eficiencia y brindar una satisfacción superior al cliente. Adoptar las capacidades de Opcenter APS dentro de Smart Factory MOM es una decisión estratégica para los fabricantes que buscan optimizar sus procesos de producción, adelantarse a la competencia y prosperar en la era de las fábricas inteligentes.
¿Listo para agregar Smart Factory a su cartera y diferenciarse de la competencia? ¡Programe una cita con nosotros hoy para platicar cómo podemos asociarnos!
AGENDAR UNA CITA