Data analytics is an essential part of modern manufacturing, facilitating real-time insights, process optimizations, predictive maintenance, and numerous other benefits. This blog post explores how data analytics in manufacturing can revolutionize every aspect of your connected factory.
The industrial sector has undergone rapid expansion, driven by Industry 4.0 and recent technological advancements. The global smart manufacturing market is projected to grow at a compound annual growth rate (CAGR) of 13.1%, rising from $277.81 billion (in USD) in 2022 to $658.41 billion in 2029. Tools for data analytics are a crucial element of the smart factory.
The manufacturing industry of tomorrow revolves around a networked factory, where each component and device can communicate with one another, providing enhanced process visibility. This vision is realized through intelligent sensors and devices connected to machine software and applications via the Industrial Internet of Things (IIoT).
A fundamental aspect of the connected factory is the application of data analytics in manufacturing. Technologies enable automatic and seamless information sharing among people, robots, and sensors on the shop floor, contributing to intelligent manufacturing. Connected equipment generates massive volumes of data, and with edge computing and connectivity, these data can be transformed for analysis and comprehension.
Real-time information facilitates comprehensive insights into diagnostic assessments, predictive maintenance, improved decision-making, and process enhancements. We delve into the advantages of data analytics for the industrial sector and how the implementation of these cutting-edge solutions can completely transform your business.
What is Analytics In Manufacturing?
Analytics in manufacturing is the foundational concept of Industry 4.0, outlining the utilization of machine data and operational systems to enhance the operations of a manufacturing company. Beyond ensuring product quality, improving decision-making, and reducing costs, this data plays a crucial role in boosting productivity and performance.
Through real-time, networked data collection, human errors are minimized, enabling quicker decision-making and process modifications, thereby revolutionizing the manufacturing sector. The adoption of this technology can be the differentiator between success and irrelevance in the current globalized and competitive industry. Companies can align more effectively with their business objectives by gaining better insight into key performance indicators.
How Can You Benefit From Manufacturing Analytics?
Manufacturing analytics offer real-time contextual awareness, digitizing the business and delivering a competitive edge to decision-makers by optimizing costs, enhancing quality, accelerating innovation, and redefining the customer experience. Manufacturing organizations are leveraging factory analytics to make sense of extensive data volumes, thereby enhancing the profitability and productivity of their operations. By employing machine learning models and data visualization tools, manufacturers can extract insights from their data, streamline workflows, and improve efficiency. The establishment of a continuous stream of data gathering and sharing enables greater agility, efficiency, and flexibility.
Improved productivity and predictive maintenance
In modern manufacturing, where people and machines work alongside each other, the seamless functioning of every machine and process is crucial for business success. A single mistake can have a significant impact on your bottom line and overall production. Utilizing the correct analytics tools ensures continuous performance by providing regular notifications and remote monitoring.
The integration of IoT-enabled sensors and edge technologies with predictive maintenance transforms your staff from problem solvers to proactive fixers by alerting them to issues before they impact production. Reporting dashboards powered by real-time manufacturing analytics enable a comprehensive check of asset and process statuses in one place. Rather than waiting for equipment breakdowns, manufacturers can conveniently schedule maintenance and prevent unplanned downtime through the use of predictive maintenance. This not only enhances the overall dependability and efficiency of the production process but also reduces expenses associated with unscheduled maintenance and equipment breakdowns.
Superior quality of services
To keep up with the swift changes in consumer expectations in recent years, access to customer intelligence and data is now more crucial than ever for manufacturing businesses. They must maximize supply chain management and generate high-profit yields, made possible through data analytics.
Instant insights enable the prediction of future trends and client demand by considering seasonality, market fluctuations, and other factors. With the help of intelligent technologies, services and output can be enhanced by sorting through data, analyzing important outcomes and numbers, and producing insightful reports. Better estimations and planning become possible; for instance, with Predictive analytics for manufacturing, you’ll better grasp how long each task takes, how much it costs, and what supplies are required.
Equally important are the advantages in terms of customer service. Knowing your customers better helps you respond to their evolving demands, build stronger bonds, and strategically modify procedures to achieve higher standards.
Lower expenses
Sophisticated analytics technologies can expedite the identification of cost-cutting opportunities at your company. The sharing of data among different, unconnected devices creates swarm intelligence, a popular IoT application commonly used in factories to aid in scheduling production, reduce bottlenecks, and enhance productivity. Through the utilization of this technology, your production can achieve cost savings through improved safety, efficiency, and predictive maintenance, while also generating net new revenue from value-added services.
Data helps identify areas ready for automation, leading to reduced waste, increased productivity, lower costs, and improved satisfaction. Real-time analytics over time provide a comprehensive insight into your manufacturing processes, highlighting areas of significant cost savings that may have otherwise gone unnoticed.
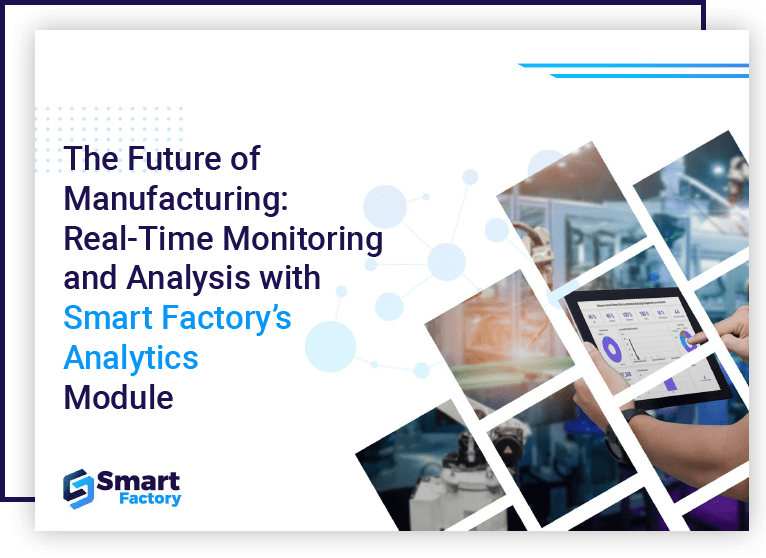
Power Up Your Production Processes With Smart Factory's Dynamic Analytics Module
Don’t let poor visibility, ineffective inventory management, and lack of machine control hold you back. Take advantage of the Smart Factory Analytics module today and transform your production processes.
Principal Commercial Justifications For Manufacturing Analytics
Some of the core commercial justifications for integrating manufacturing analytics into your business are mentioned below:
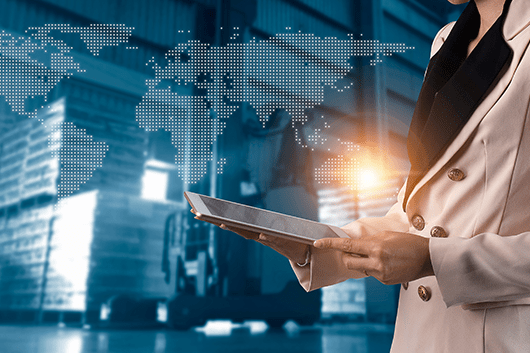

Chain of supply
- Demand projections
- Order processing
- Inventory management
- Performance of suppliers
- Analytics for transportation
- Systems of early warning
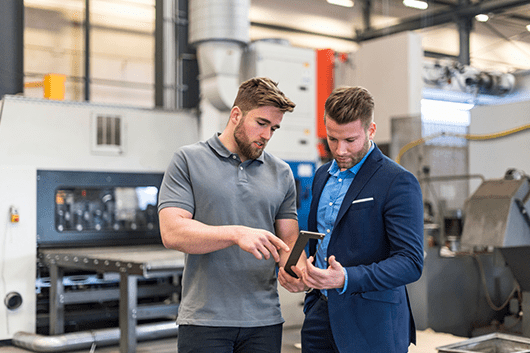

Product competent
- Instantaneous quality assurance
- Primary reason
- Dependability
- Guarantee
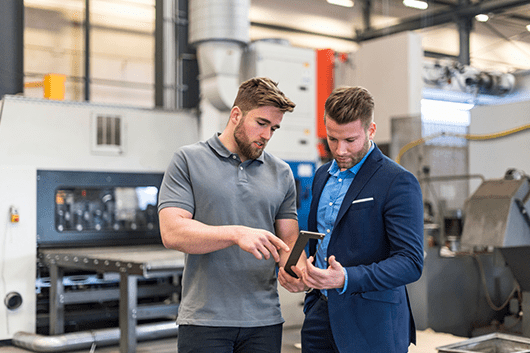
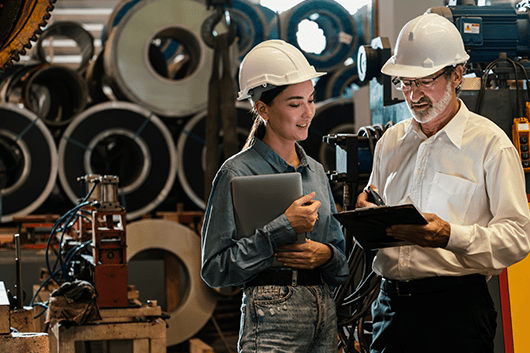

Field Assistance & Maintenance
- Inventory control
- Performance of suppliers
- Analytics for transportation
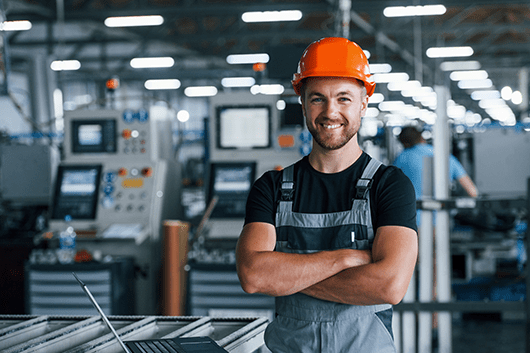

Building a productive factory
- Equipment and process monitoring in real-time
- Process ability
- Maximise upkeep
- OEE and manufacturing output
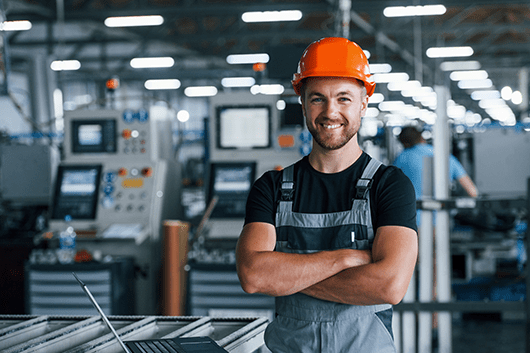
The Journey of Manufacturing Analytics: From Insights to Action
But how can these commercial objectives be achieved? The manufacturing analytics journey aims to transform the information gleaned from your production data into insights that can subsequently be translated into business-enhancing decisions.
- The first step in the process is to identify the business use cases. Most manufacturers strive to achieve similar goals, such as increasing income, building an effective factory, and enhancing the quality and dependability of their products. Let’s take a left-to-right tour of the process to discover how to implement your manufacturing insights.
- Assembling the data is the next stage of the process after initially determining the business use cases. Unfortunately, a lot of data comes from connected devices, sensors, and the factory floor in the manufacturing industry, and this data frequently exists in silos. Additionally, you get data about suppliers, procedures, machinery, sales, and more. You must gather the data, combine it, clean it, filter it, if necessary, and generally get it ready for analysis with data analytics in the manufacturing industry.
- After that, you may begin automating procedures to search the data for signals like yield, downtime, warranty claims, and faults. After conducting some preliminary research, you might determine that there are a few typical viewpoints you want to adopt. Applications for real-time monitoring and dashboards that can be applied again to different kinds of data can be made.
- You can create models for additional prediction-based analysis using sophisticated analytics software beyond simple dashboards. Product measurements, pressure, and temperature readings could be some of your input data. Models can be used to verify or forecast production levels, equipment malfunctions, and product quality.
The Objectives of Manufacturing Analytics
Manufacturing analytics aims to transition from straightforward descriptive data collection and display to real-time predictive data utilization. This evolution facilitates the identification of equipment and process problems, cost reduction, and optimization of efficiencies across the supply chain with minimal risk and overhead. Manufacturing analytics makes this information available to all employees, from the CEO to the shop floor worker.
The final output of a business can be significantly enhanced with the aid of manufacturing analytics. Various procedures, including data-driven product optimization, defect density level management, and analysis of purchase patterns and customer feedback, contribute to this improvement. Tools such as IoT sensors and machine learning models are employed for data-driven product optimization, allowing manufacturers to optimize production based on various variables.
By carefully examining how products are used, manufacturers can alter components to achieve higher usage rates. Maintaining a low defect density ratio is crucial, and manufacturers can now better identify process conditions that result in higher fault densities through data gathered from digital factories. Customer analytics enables understanding clients’ purchasing patterns and lifestyle preferences, helping manufacturers produce and offer what customers genuinely desire based on information about future purchase habits.
Manufacturing analytics contributes to raising both production yield and throughput. Anomaly detection is a primary method for achieving this. Factory supervisors can address problems swiftly without compromising output by using anomaly detection to notify them of product flaws early in production. Anomaly detection utilizes a combination of Internet of Things sensors, historical data, and machine learning algorithms to identify anomalous data indicating an impending issue.
Furthermore, analytics for manufacturing can lower the costs and hazards of equipment failures or downtime. This is achieved by identifying unprofitable production lines or bottlenecks and through predictive maintenance of essential assets, foreseeing breakdowns, and minimizing machine downtime.
To Sum Up
Businesses should adapt to the changing times by embracing analytics in the industrial sector, transforming the company landscape, and safeguarding against potential threats. The path of Industry 4.0 has already been set, and the question is not whether businesses will use analytics but when they will implement business intelligence. Analytics represents the final step on the road to Industry 4.0; without it, the information gathered by intelligent IoT devices is essentially meaningless. As adoption increases, businesses that embrace analytics are gaining a competitive edge. Despite having one of the highest rates of BI adoption, the manufacturing industry still has a long way to go.
While major brands in the sector have embraced IoT and analytics, smaller and medium-sized businesses need to catch up. With innovations like cloud computing and analytics-as-a-service, businesses no longer need to make large upfront investments in analytics. They can simply try it to discover the potent insights and advantages it may bring, then expand their use. This is where the Smart Factory MOM solution comes into play. It empowers organization users with the capability of self-service analytics, enabling them to comprehend their data and make timely decisions critical to their organization’s success. Undoubtedly, the future is data-driven, and those prepared for it will succeed. Trusting equipped technologies, such as the Smart Factory MOM solution, for guidance ensures access to innovative industrial solutions and tools for targeted data analytics, ultimately improving company results.
Contact us today to learn more about how we can help you implement, train, and maintain the Smart Factory MOM solution and count on us to help you overcome any hurdles along the way.