Manufacturing businesses constantly seek ways to improve production efficiency to gain a competitive edge. This drive for efficiency extends across the entire supply chain and factory floor, where maximizing available assets is key to minimizing waste and achieving optimal production output.
Improving production efficiency brings numerous benefits, including increased profits, enhanced employee safety, and a satisfied customer base. However, it is essential to differentiate between productivity and efficiency. Merely focusing on productivity and attempting to streamline operations by removing essential elements may jeopardize employee safety and compromise product quality.
To truly enhance production efficiency, manufacturers must adopt a holistic approach that leverages existing resources, implements smart technologies, and optimizes processes without sacrificing quality or safety. By doing so, businesses can realize significant gains in efficiency and elevate their overall performance in the market.
Below are a few tips manufacturers can employ to improve their production line efficiency and product quality.
Tip #1: Begin With a Hard Look at First Time Yield (FTY)
To achieve optimal production line efficiency, it is crucial to closely examine the concept of First Time Yield (FTY) at each station along the production line. As the number of stations increases, so does the need for a data-driven quality assurance process that ensures FTY approaches 100% at every stage.
First Time Yield (FTY) is a metric used in manufacturing to measure the percentage of products or units that pass all quality checks and meet the required specifications during their initial production run, without the need for rework or repair.
Let’s consider a hypothetical scenario with a production line consisting of 50 stations, each operating with an average FTY of 99%. While 99% might seem impressive, the cumulative effect of slight variations along the line becomes apparent. The Rolling Throughput Yield (RTY) at the end of the line drops to approximately 60%, resulting in a significant scrap or rework rate of 40%. This translates to substantial financial losses for the manufacturer.
Rolling Throughput Yield (RTY) is a metric used to measure the overall yield or success rate of a multi-step or multi-stage process. It evaluates the cumulative performance of the entire process by considering the individual yields at each step. To calculate the Rolling Throughput Yield, the yield at each station or step along the process is multiplied together.
Case Study to Showcase Boosted FTY
A compelling case study showcases the impact of boosting FTY from 90% to 98%, enabling annual savings of over $3 million. Suppose, we examine a product with a manufacturing cost of $5,000, divided equally between material costs and transformation costs. With an annual target production run rate of 10,000 units and an overall FTY (or RTY) of 90%, the manufacturer would need to initiate production of 11,112 units to achieve the desired output due to failed units. This results in $5.6 million worth of scrapped products, reflecting a significant waste of resources. The total cost per unit also increases from $5,000 to $5,556.
Let’s assume the manufacturer implements a rework process that successfully recovers 80% of the failed units, thus boosting the overall yield from 90% to 98% while maintaining the FTY at 90%. Although the rework cost is 50% higher than the initial transformation cost, amounting to $3,750 per unit instead of $2,500, it is a worthwhile investment considering the commitment of $5,000 per failed unit. The total rework costs amount to $3.8 million annually, increasing the average production cost per unit from $5,000 to $5,485.19.
Now, imagine achieving the same yield increase from 90% to 98% without the need for costly rework. This would result in an average production cost per unit of $5,102.04, translating to a savings of $383.15 per part. Consequently, the total savings amount to approximately $3.83 million per year.
The challenge lies in identifying the necessary productivity improvements at each station along the line to drive the desired increase in FTY. This is where Smart Factory’s production data collection and monitoring capability is crucial. The Smart Factory Manufacturing Operations Management (MOM) Production module enables manufacturers to monitor and optimize processes and ensures enhanced FTY and overall production line efficiency.
Tip #2: Early Defect Detection
Detecting defects as early as possible in the production process is crucial for improving FTY and overall production line efficiency. The closer to the point of origin that a production flaw is identified, the less disruptive it will be to the entire production process, resulting in lower costs and minimized waste.
However, many manufacturing lines still rely on traditional testing, inspection, and quality control methods that primarily focus on end-of-line testing. This approach can lead to significant time, money, and material investments in parts or sub-assemblies that may ultimately need to be scrapped.
To achieve substantial quality gains and improve overall efficiency, it is essential to shift the focus from solely relying on a final quality check to implementing checks and balances at every critical juncture as a part or assembly progresses along the production line.
“Early defect detection is crucial for improving product quality and minimizing waste. By implementing effective quality control measures at the earliest stages of production, manufacturers can reduce rework, scrap, and customer complaints, leading to higher customer satisfaction and increased profitability.”
– The International Organization for Standardization (ISO)
This approach is commonly known as in-process testing. In-process testing involves conducting inspections, measurements, and quality assessments at various stages of the manufacturing process. By integrating quality control measures throughout the production line, manufacturers can detect and address defects early on, preventing them from progressing further downstream and reducing the need for costly rework or scrap.
In-process testing ensures that potential issues are identified and addressed at the earliest possible stage, minimizing the impact on subsequent production steps and increasing the chances of achieving a high FTY. This approach empowers businesses to take a proactive stance in quality assurance, ensuring that potential defects are detected and addressed early, leading to a smoother and more efficient manufacturing process.
Tip #3: Harnessing Part Production Data for Quality Improvement
When a defect is detected, or a part fails a quality check, the next step is to understand the root cause of the issue. The key to gaining real value from your part production data lies in collecting and analyzing the right data.
Let’s consider an example: a part that has failed a leak test. This part has undergone various processes such as drilling, clamping, dispensing, and welding at previous stations. The failure in the leak test could be attributed to a flaw in one or more of these processes.
By utilizing the appropriate sensors and software, you can equip existing process stations on the production line with intelligent tools to collect, correlate, and visualize highly granular part production data. It’s important to note that this data is generated by the part itself, not just the machine, during a process or test cycle.
By examining the problem from the perspective of the part, rather than solely focusing on the specific station, you can gain more effective and actionable insights. Analyzing the part production data allows you to identify patterns, anomalies, and correlations that may contribute to defects or quality issues.
For instance, by analyzing the data from the drilling, clamping, dispensing, and welding processes, you can pinpoint any deviations or abnormalities that might have led to the failed leak test. This level of granularity enables you to identify the specific process or processes that require improvement or adjustment to enhance overall quality.
Collecting and analyzing part production data provides valuable insights into the performance of individual processes and their impact on the final product. It empowers manufacturers to make data-driven decisions, optimize processes, and implement targeted improvements that address the root causes of defects or quality issues.
By considering the problem from the perspective of the part and leveraging comprehensive data analysis, manufacturers can unlock real value from their part production data.
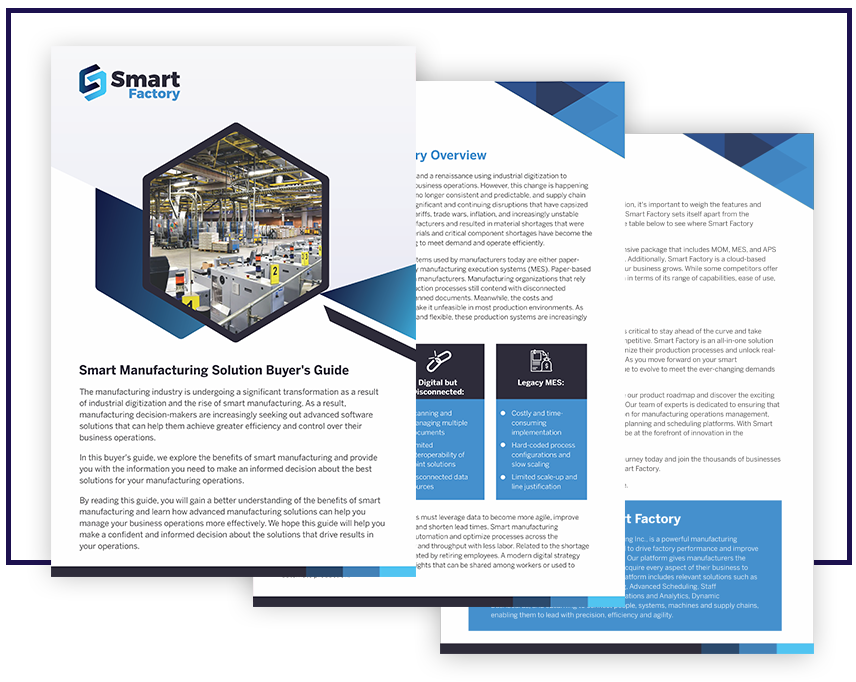
Optimize Your Production Process With Our Production Module
Tip #4: Analyze Workflow Efficiency in the Factory
Improving efficiency in a manufacturing operation requires carefully examining the workflow to identify bottlenecks and areas that hinder productivity. Smart Factory MOM solution tracks and analyzes production data to gather relevant workflow metrics and identify areas for improvement.
It simplifies production tracking and provides comprehensive data for analysis, enabling businesses to monitor each production stage effectively. By leveraging real-time data from various sources, such as machine sensors, Internet of Things (IoT) devices, and production equipment, the Smart Factory MOM solution captures detailed information about the production process.
With the collected data, manufacturers can gain valuable insights into the performance of individual stations, identify bottlenecks, and detect areas where efficiency is being compromised. By analyzing key workflow metrics, such as cycle times, throughput rates, and equipment utilization, Smart Factory MOM helps to identify specific stages or processes that contribute to inefficiency.
Tip #5: Upskilling the Workforce for Enhanced Production Efficiency
Improving production efficiency does not necessarily imply replacing employees with machines through extensive lean manufacturing practices. Instead, businesses can focus on upskilling their workforce to effectively collaborate with technology and optimize productivity.
Beyond basic equipment operation, it is essential to provide employees with comprehensive training that encompasses newer, safer, and more efficient practices across all stages of the manufacturing operation. By investing in their professional development, businesses can empower employees to perform at their best and contribute to improved production efficiency.
Identifying skill gaps and designing standardized operating procedures is crucial in enhancing the productivity and efficiency of the workforce. These procedures should align with industry best practices and be tailored to the specific needs of the manufacturing operation. By establishing clear guidelines and expectations, employees can understand their roles and responsibilities, ensuring consistent and high-quality performance.
Businesses can leverage Smart Factory’s e-learning module to facilitate the upskilling process. This module provides on-the-go training and learning resources, accessible to employees anytime and anywhere. Through interactive modules, instructional videos, and assessments, employees can acquire the necessary knowledge and skills to enhance their understanding of production processes, technology implementation, and best practices.
By investing in upskilling initiatives and providing ongoing training opportunities, businesses create a culture of continuous learning and improvement within the workforce. Employees become more adaptable, proficient, and equipped to embrace new technologies and optimize production efficiency. This approach enhances employee satisfaction and engagement and leads to higher productivity and overall operational success.
Wrapping up
Improving production line efficiency in 2023 requires a strategic and data-driven approach. Manufacturers can make the most of their investments by leveraging the capabilities of their current equipment and systems. By implementing data-driven approaches and harnessing the wealth of information available, businesses can uncover hidden insights and identify optimization opportunities that were previously overlooked.
Manufacturers are encouraged to adopt the Smart Factory MOM solution to support these efforts. Smart Factory MOM provides advanced tools for tracking, analyzing, and optimizing production data in real-time. By integrating with existing equipment and systems, Smart Factory MOM enables manufacturers to make data-driven decisions, optimize workflows, and drive continuous improvement.
Ready to add Smart Factory to your portfolio and differentiate yourself from competitors? Schedule an appointment with us today to discuss how we can partner up!