Navigate to section

What Is Changeover Time In Manufacturing?
Examples of Changeover Time and Its Impact in the Manufacturing Process
Industry Type | Product | Number of Products That Would Stop Production in 100 Hours | Average Cost of the Affectation (USD) |
---|---|---|---|
Automotive | Automobiles | 100 vehicles | $2,000,000 |
Electronics | Smartphones | 50,000 phones | $500,000 |
Food and Drinks | Water bottles (500 ml) | 200,000 bottles | $150,000 |
Textile | T-shirts | 25,000 t-shirts | $75,000 |
Construction | Cement blocks (unit) | 50,000 blocks | $60,000 |
Pharmaceutical | Medications (tablets) | 500,000 tablets | $250,000 |
Metalworking | Machinery parts | 5,000 pieces | $200,000 |
Chemistry | Plastics (tons) | 50 tons | $100,000 |
Energy (Renewable) | Solar panels | 1,000 panels | $300,000 |
Aerospace | Airplane components | 10 units | $1,500,000 |
Shopfloor (Manufacturing Industry) | Electronic components (PCBs) | 100,000 printed circuits | $400,000 |
Rubber and Plastics | Tires (unit) | 25,000 tires | $300,000 |
Packaging | Cardboard boxes (unit) | 150,000 cardboard boxes | $80,000 |
Changeover Time Measurement Formula and Calculation
Calculation of Change Over Time
- General Formula
- Detailed Formula
Changeover time Practical Breakdown Example
- Preparation of materials (transport to the consumption area): 7 minutes
- Preparation of tools (mixing blades): 6 minutes.
- Inventory review (proteins): 10 minutes.
- Preliminary adjustments on the machine (technical preparation of times): 15 minutes.
- Tool change (removal and placement of blades): 10 minutes.
- Cutter cleaning (removal, disinfection, sanitizing): 27 minutes
- Final adjustments on the machine (calibration): 15 minutes.
- Initial quality tests (blade rotation test): 10 minutes.
The 7 Steps to Improve Change Over Time by SMED Methodology (Single Minute Exchange of Die)
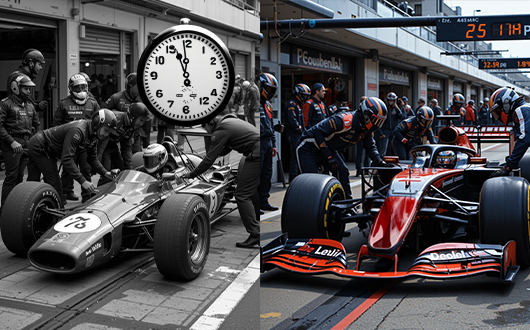
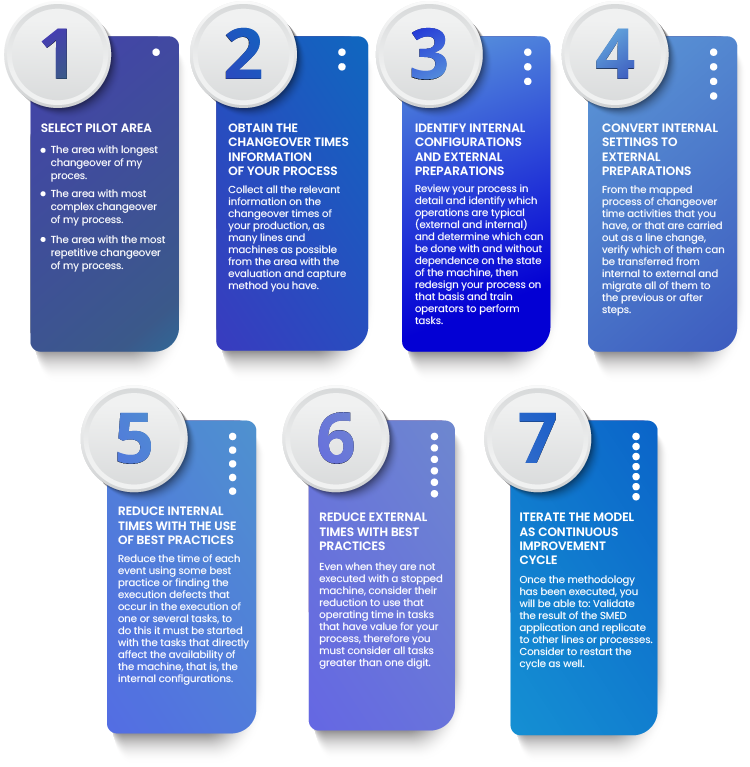
Process Improvement
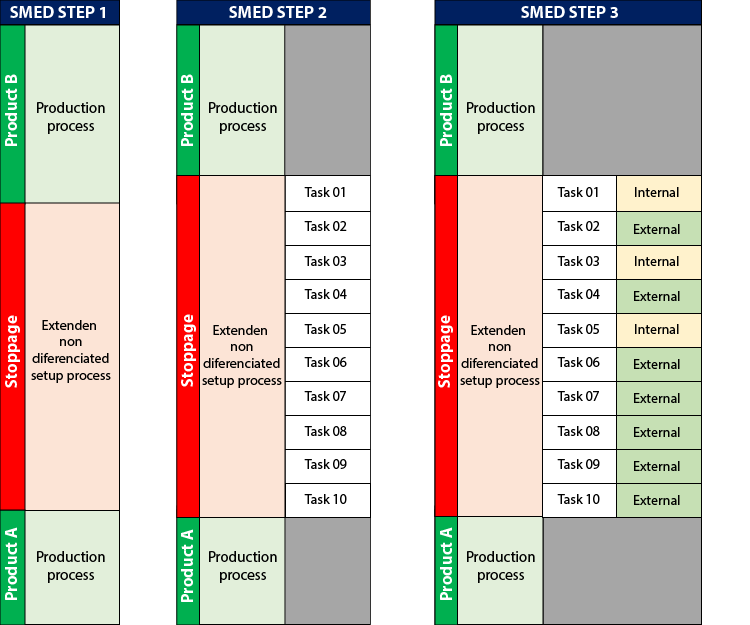
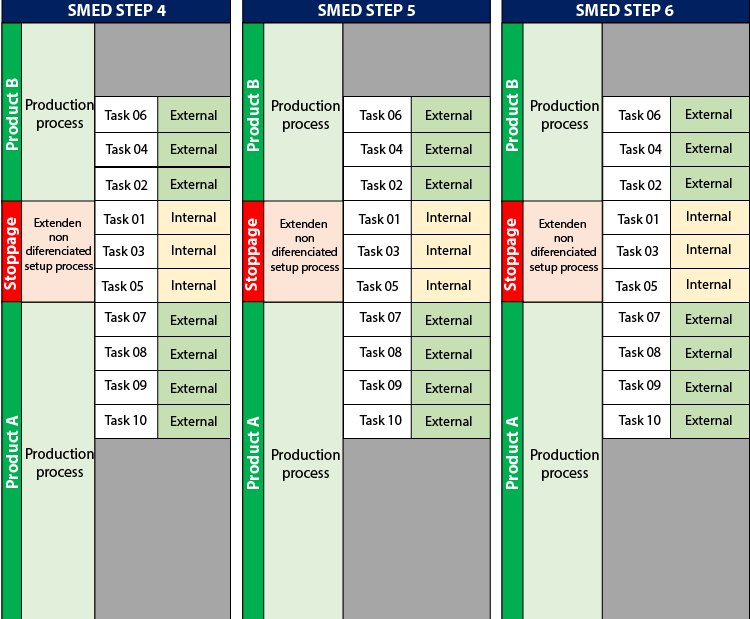
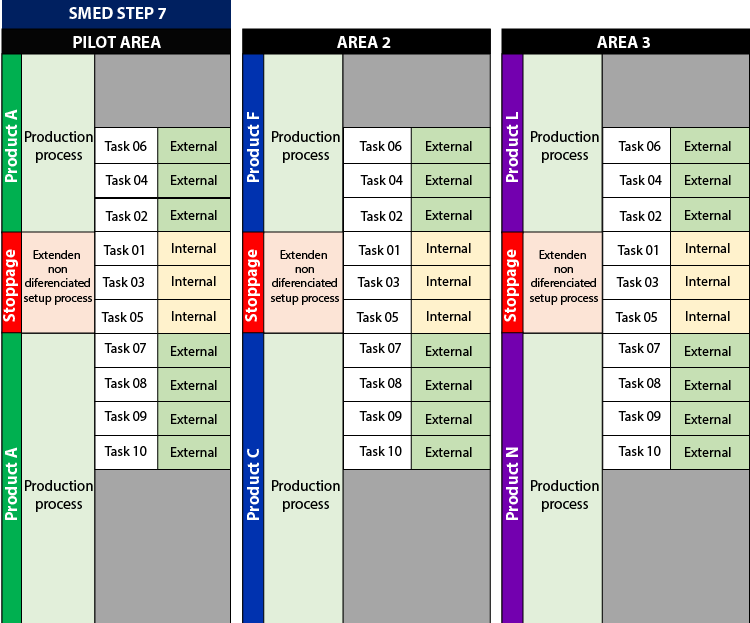
10 Best Practices to Control or Reduce Your Changeover Time
1. Implement Real-Time Monitoring Technology
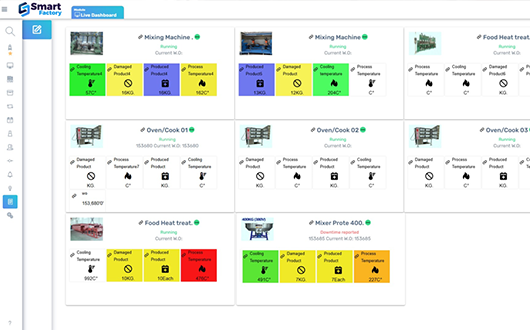
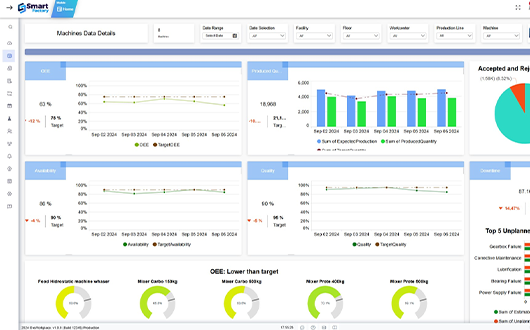
2. Predictive Analytics Dashboards
3. Standardize Work Procedures
- Updated versions available at all times
- Graphic information or information supported by images or video
- Define clear, step-by-step instructions
- Always consider troubleshooting
- Maintain checklists and timing guidelines
- Use response-based addressing and electronic systems (electronic SOPs)
- Review and update these procedures on an ongoing basis to reflect any improvements
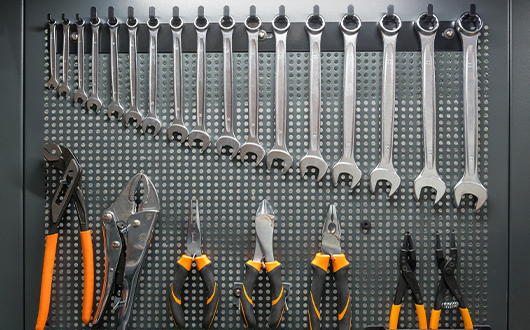
4. Organize and Standardize Tools and Materials
Best Practice Tip: Use smart identification and storage techniques, such as fail-safe shadow boards (Pokayoke Shadow stands), tool racks, and shared or exclusive materials organization systems, to ensure that both tools and components are in the right place and can be easily accessible.
5. Use Quick Change Equipment
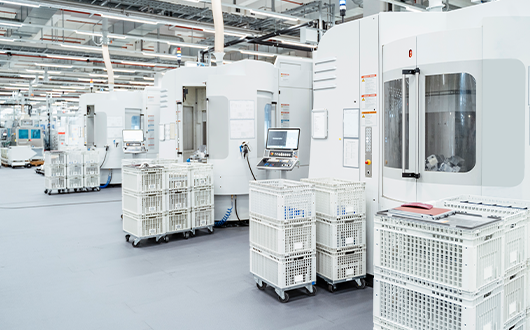
6. Perform Time of Change Audits
Best Practices Tip:
- Conduct Gemba walkthroughs on the production floor where you and your team identify possible steps that are not necessary or have no apparent value that may have areas for improvement.
- Use data analysis tools such as dashboards and information boards that show information visually to track and analyze times of change. Try to ensure that these dashboards offer at least identification of trends, patterns and recurring problems.
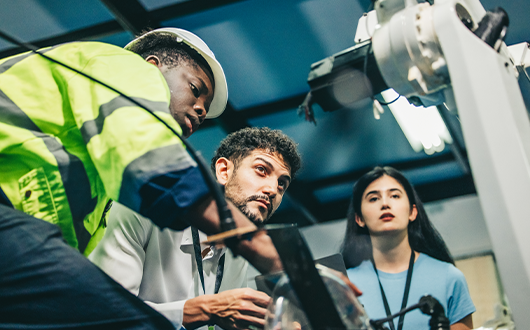
7. Involve Employees in Continuous Improvement
8. Implement Preventive Maintenance
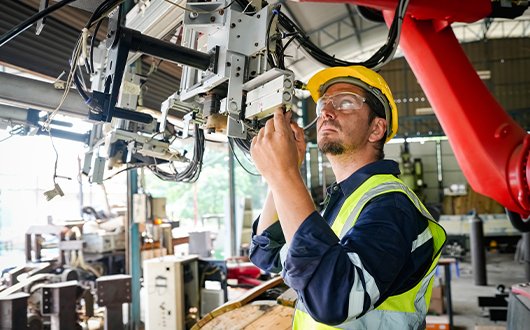
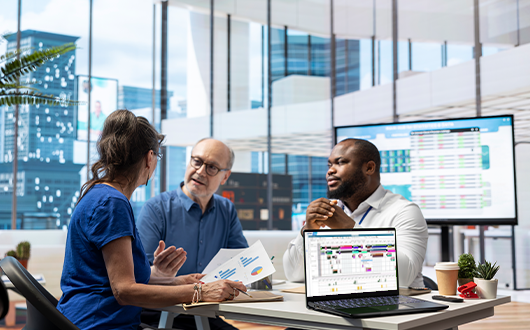
9. Optimize Production Scheduling and Planning
10. Train and Train Employees
- Use or apply accelerated learning methods such as e-learning systems.
- Train operators to operate multiple machines and prevent delays caused by staff shortages.
- Have personnel with cross-skills (cross-training of employees on multiple machines or processes) which will ensure greater flexibility of personnel for possible interventions or needs.
The Role of Smart Factory MOM as a Software to Reduce Changeover Times

Real-Time Monitoring (IIoT Systems)
Through the use of information technologies like machine communication, sensors, and IIoT devices, MES and MOM systems collect real-time data about the condition of machines and processes with continuous monitoring, to highlight potential issues, trigger early warnings to minimize unexpected downtime, and identify improvement opportunities.

Scheduling Optimization (APS Systems)
Advanced Production Scheduling (APS) systems, integrated with MOM software, utilize sophisticated algorithms to optimize production planning.

Digital Instructions (e-SOPs)
Digitalized work instructions or e-SOPs are vital for task execution. This reduces training time, minimizes errors associated with outdated or misunderstood instructions, and allows operators to execute changeover tasks without extensive training, with clear, visual, and data-capturing instructions.

Simulation and Predictive Analysis (Dashboards and Andon Boards)
Advanced manufacturing software like Smart Factory MOM offers simulation models that test different production scenarios to identify the most efficient configurations.

Improved Communication and Collaboration (Data Sharing and Notifications)
Integrating functions like production, planning, inventory, and logistics into a single manufacturing software (MOM or MES) facilitates coordination across departments.

Automated Inventory Management (Materials and Tools)
Integrated MOM-ERP or MES-ERP systems offer automated inventory management, ensuring tools, raw materials, and consumables are available on time without manual intervention.